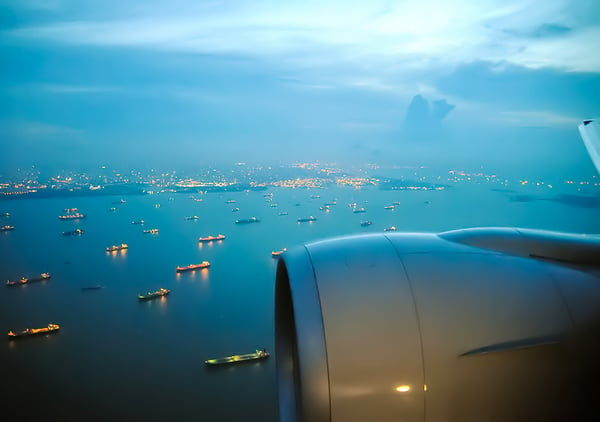
Engine Off-Wing? Understanding What Triggers an Aircraft Engine Removal
Aircraft engines are marvels of modern engineering, designed to operate reliably under extreme conditions. Yet, even these sophisticated machines require periodic removal for maintenance and overhaul. For airlines and maintenance ...
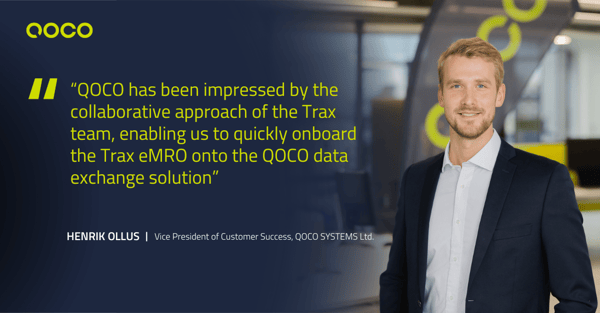
QOCO welcomes Trax as the next M&E system onto the QOCO data exchange solution for Rolls-Royce
ESPOO, Finland (April 9th, 2025) QOCO Systems, is delighted to announce Trax as the latest addition to connect to QOCO’s solutions, utilized by Rolls-Royce for its engine services. The Rolls-Royce and QOCO partnership began in ...
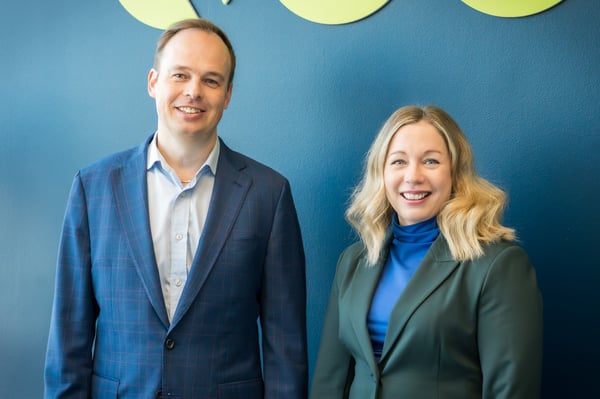
QOCO Systems expands its board with seasoned industry professionals
QOCO Systems welcomes Vesa Paukkeri and Emma Aidanpää-Salmi to the board as the company continues its aggressive growth within the aviation maintenance industry. The addition follows an announcement to increase staff with over ...
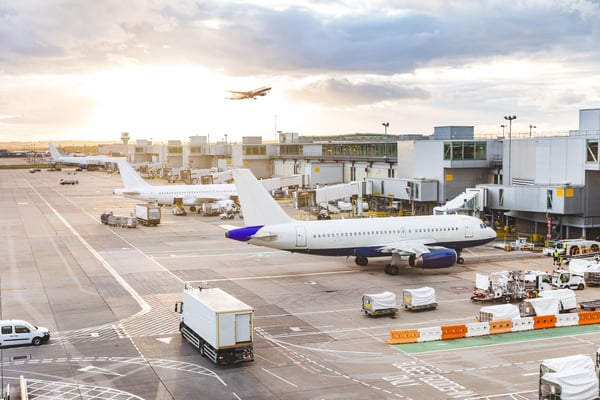
Synchronizing MRO software with airline ERP systems
Introduction At QOCO, we specialize in aviation maintenance software. Over the years, we’ve worked closely with airlines, OEMs, and MROs, and one thing has become crystal clear: disconnected systems can significantly hinder ...
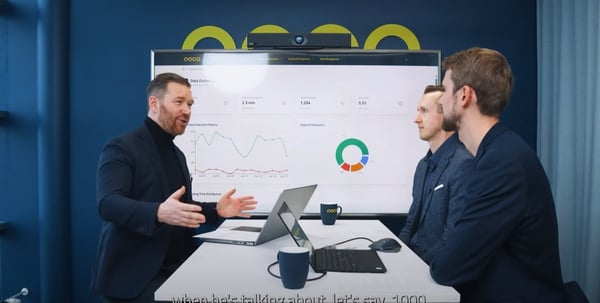
Webinar: How Engine MROs can benefit from Aviadex
Webinar: How Engine MROs can benefit from Aviadex
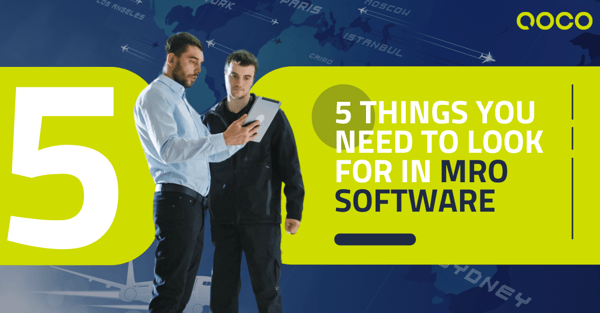
5 Things You Need to Look for in MRO Software
Driven by technological advances, digital transformation and increasing regulatory requirements, the aviation maintenance industry is growing rapidly. Gains for MRO from digital solutions have become evident, allowing for ...