Optimizing Engine Lifecycle: Lufthansa’s Partnership with Rolls-Royce and QOCO
Lena Duken, Airworthiness Engineer at Deutsche Lufthansa AG, and Jeff Winter, Senior Consultant at Lufthansa Industry Solutions AS GmbH, tell us about a double implementation to ensure optimum time on wing for their Rolls-Royce engines.
This article is a case study of how QOCO has enabled a continuous data exchange between Lufthansa and Rolls-Royce Digital Services. That said, it is always useful when sharing a case study such as this, for readers to understand something about the business to which the implementation has been applied. So, first, some information about Lufthansa and Lufthansa Industry Solutions.
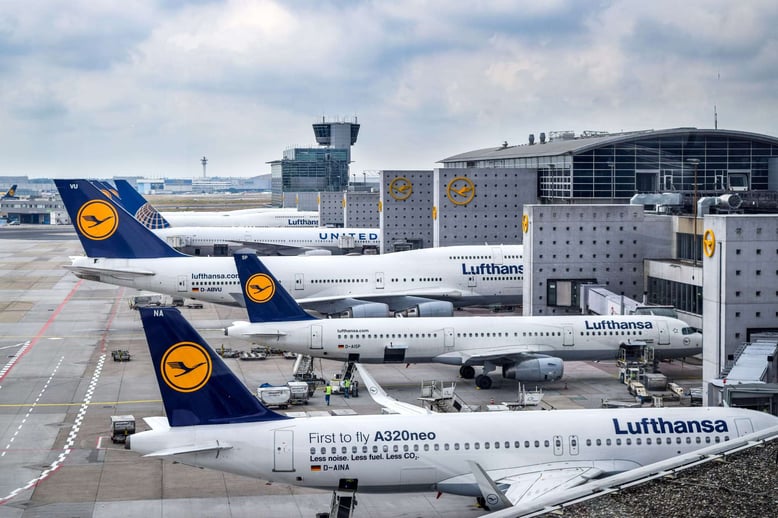
Lufthansa and Lufthansa industry solutions
Lena is part of the business department with some thirty airworthiness engineers who undertake everything related to fleet lifetime control. That includes requirements for the engines when they have to be taken off the wing or when which part has to get what type of sub-task, plus everything regarding standard duty cycle counters for the Trent XWB engines on the Airbus A350 aircraft; this case study is specifically about the Airbus A350 and Trent XWB engines.
QOCO, in collaboration with Lufthansa Industry Solutions, AMOS, as their new MRO/M&E IT solution. Introducing that new IT solution in May 2022 was a significant and ambitious project for Lufthansa. Jeff works with Lufthansa Industry Solutions, a Lufthansa company delivering IT services for various customers in air travel, logistics, transport, and more, with locations in Germany, Switzerland, Albania, and the USA, and with more than 2,300 employees. Jeff’s role is to deliver a consultancy experience based on AMOS and other IT applications to the customer.
Transition to AMOS and Aviadex: Streamlined Data Exchange for Better Performance
Prior to the arrangement in this case study and the introduction of AMOS from Swiss Aviation Software (Swiss-AS), Lufthansa was using an in-house IT solution developed by Lufthansa Technik to manage MRO/M&E activities. Together with Rolls-Royce and Lufthansa’s own IT department, Lufthansa Technik had developed a customized interface to execute the data exchange between the A350 fleet and Rolls-Royce.
After careful consideration, the airline started to think about how to enhance the current interface and utilize the in-house resources more efficiently. Rolls-Royce and QOCO worked with Lufthansa in defining firm solution specifications and implementing a seamless data exchange — Aviadex.
“The initiator of the change was the introduction of AMOS. The implementation of a new MRO/M&E IT system enabled Lufthansa to get a new way of managing data exchange.”
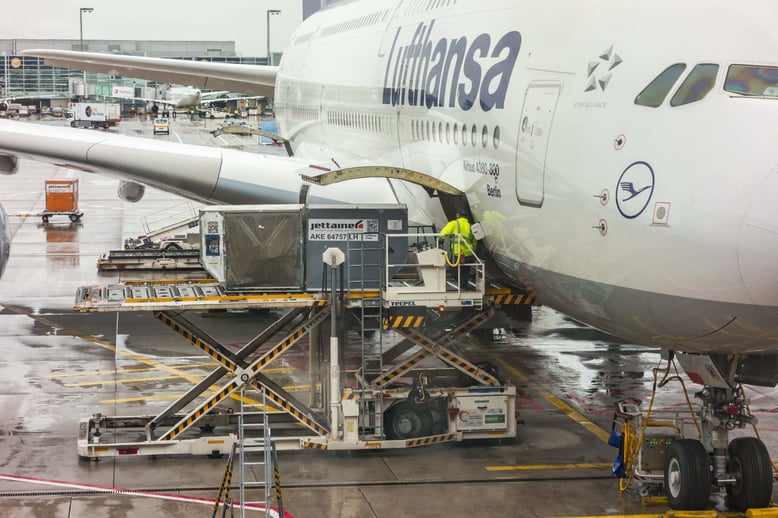
The initiator of the change was the introduction of AMOS. The implementation of a new MRO/M&E IT system enabled Lufthansa to get a new way of managing data exchange. DACs (Direct Accumulation Counts), used by Rolls-Royce for lifting Trent XWB engines, allow the engines and engine components to be monitored based on the actual wear and tear on the engines, resulting in extended time on-wing. As Lufthansa already had an interface with the Rolls-Royce system up and running, significant changes were not required. QOCO’s role was to help Lufthansa set up a bi-directional flow of data from Lufthansa’s AMOS system to Rolls-Royce DACs and back in order to integrate the AMOS system with the Rolls-Royce service, an integration that had not been there before.
The solution and its implementation
Aviadex by QOCO is an automated data exchange platform which helps operators and, as in this case, the OEM, Rolls-Royce to exchange data. The solution manages the bi-directional data flows between Lufthansa and Rolls-Royce systems (Figure 1).
In addition, QOCO does comprehensive data controls and data validations to promptly alert the airline to any data issues. Aviadex is always running in the background and keeping the AMOS and Rolls-Royce systems synchronized but invisible to users. After the implementation, QOCO provides a fully managed service that ensures undisrupted continuous data exchange, validates data quality and fulfills set requirements.
The project implementation
The implementation of the solution for Lufthansa IT was a quick and easy one since QOCO delivered documentation to Lufthansa along with examples, tests and more. Fifteen interfaces had to be updated from the AMOS system in the Lufthansa IT environment.
We opted for a ‘big bang’ go-live (see above) so everything had to go online in just a few hours which was not that easy. During the migration, the standard duty cycle counters that go with the Trent XWB also had to be migrated plus, also before the go-live, it was necessary to adjust processes with some tiny changes that had to be done in AMOS. Other than that, for Lufthansa, the less we have to deal with the new solution, the happier we are as an operator and it has proved robust and reliable.

“The implementation was time critical as Lufthansa was already using the DACs System exclusively, which meant that we couldn’t afford a long delay in the data exchange, which had to be up and running reasonably quickly after the AMOS go-live.”
Due to the Covid-19 pandemic, there were no face-to-face meetings until the go-live and the following weeks. Much of the preparatory work had to be conducted remotely. Also, we have to remember that Lufthansa was implementing two new systems with both AMOS and Aviadex.
The entire project was very ambitious, and it was good to find that this part of the project was very straightforward, with not too many problems encountered on the part of the airline. For QOCO, there was more testing than is usually required with other operators because Lufthansa had to complete quite a few data migrations; as a result, the data quality analysis had to be done a couple of times to ensure that the data was good.
Also, testing standards needed to be rigorous because the airline was already using the DACs, and it was important to avoid any hiccoughs when going live. QOCO always tries to arrange its resources to be available when customers need it. The implementation was time-critical as Lufthansa was already using the DACs System exclusively, which meant that we couldn’t afford a long delay in the data exchange, which had to be up and running reasonably quickly after the AMOS go-live.
Before the project, the QOCO and Lufthansa teams agreed on the timeline: when the go-live should happen and when various stages were needed, with QOCO working around that. There were bi-weekly calls with Lufthansa, QOCO and Rolls-Royce at which test cases were discussed with the next steps forward. We also had individual test runs included in the data migrations so that, whenever Lufthansa set up an entire data migration within the scope of the AMOS go-live, we also tested the QOCO interface and QOCO made that possible. In all, there were four or five test runs for the whole process, with all the data migrated and tested for quality. Now that it’s all up and running, the automated data exchange service frees every party’s workload and lowers operational costs.
Challenges encountered
The major factor and dependency, during the QOCO Avaidex implementation project, was the ongoing AMOS MRO/M&E system implementation that was running in parallel at Lufthansa. Another important factor was that there was already an existing data exchange/integration solution in place between the Lufthansa’s previously utilized MRO/M&E system and Rolls-Royce DACs and that Lufthansa was already using the Rolls-Royce DACs.
“Lufthansa has a large fleet of twenty-one Airbus A350’s with Trent XWB engines. For this reason, managing the data exchange manually was not an option, not even as a backup solution.”
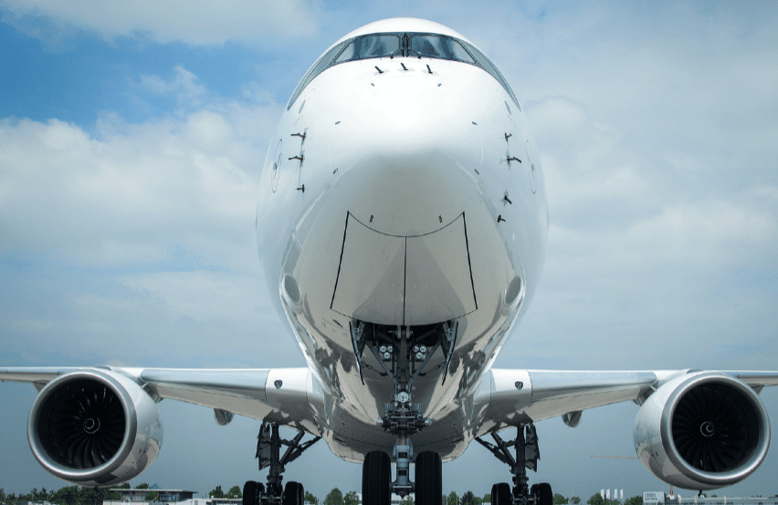
A further challenge was data quality. Data exchange testing was done in multiple iterations; data quality improved with each data migration round from Lufthansa’s old MRO/M&E system to AMOS. Some of the data quality findings were identified by QOCO’s team performing the data quality analysis (DQA) and reported to the operator. DQA is an inherent part of the implementation project. The final DQA was completed after the last data migration run just before the go-live.
The final data challenge was the sheer volume of data to be handled. Lufthansa has a large and growing fleet with currently twenty-one Airbus A350’s with Trent XWB engines and more on order. For this reason, managing the data exchange manually was not an option, not even as a backup solution. Go-live for transition, from the previous MRO/M&E system, with in-house integration with DACs, to AMOS, with Aviadex based data exchange with DACs, had to happen in just a matter of weeks after the AMOS go-live. That meant that the downtime of not having the data exchange running had to be minimized. In the event, EngineData.io end-to-end testing was completed right after AMOS go-live. After successful end-to-end testing, Lufthansa went live with Aviadex just two weeks after the AMOS go-live.
As of today, QOCO ‘s Support Team is continuously keeping an eye on the data exchange that includes comprehensive data quality controls. Possible data quality findings are immediately analyzed and reported to Lufthansa and Rolls-Royce enabling rapid corrective actions that continuously ensure the continuity of core business operations.
Key Benefits and Lessons Learned from Lufthansa’s EngineData.io Implementation
As far as working with QOCO is concerned, we would change nothing. Of course, it would always be nice to get some more testing done to get a better feeling for any new solution, but the whole project and implementation went well. Always, with big IT roll-outs, there is never the time to do everything that you might want to do, but in truth, we’d see no need to do anything differently if there were a next time.
From the QOCO perspective, the project took a while to get started, and it was necessary to wait for the AMOS implementation to get closer before this program could get underway. There were some small matters with the timeline having to change, but that was only a matter of weeks, so small adjustments in the schedule were all that were needed. The main benefit for Lufthansa, of course, is the ability to improve engine time on wing.
Future Expansion
Within Lufthansa, the interface is currently with AMOS but the plan is to have that interface working with other applications and systems. QOCO continuously extends data exchange capabilities driven by customer needs and improving Aviadex experience.