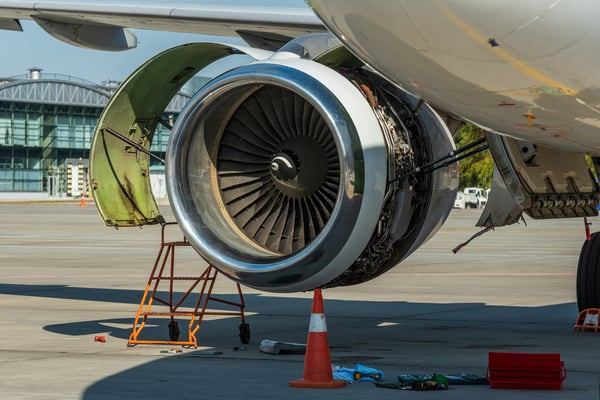
Trends and workforce challenges in aircraft maintenance
The aircraft maintenance industry is rapidly evolving due to technological advancements and shifting operational demands. Drawing from my experience in this field, I have observed key trends shaping the industry, as well as ...
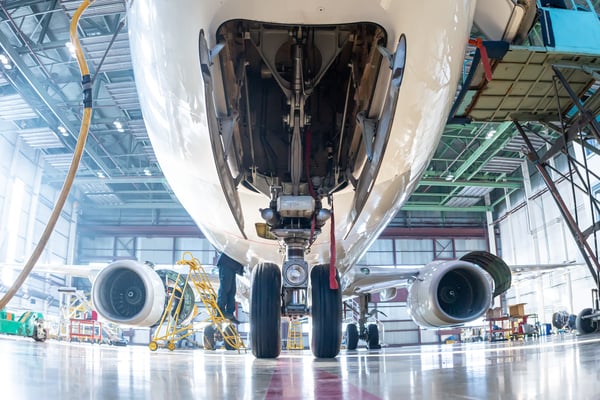
Choosing the best MRO Software
In aviation, safety and efficiency go hand-in-hand. In that mix, maintenance, repair, and overhaul (MRO) software plays a critical role. As airlines and MRO providers face increasing operational demands, the need for robust, ...
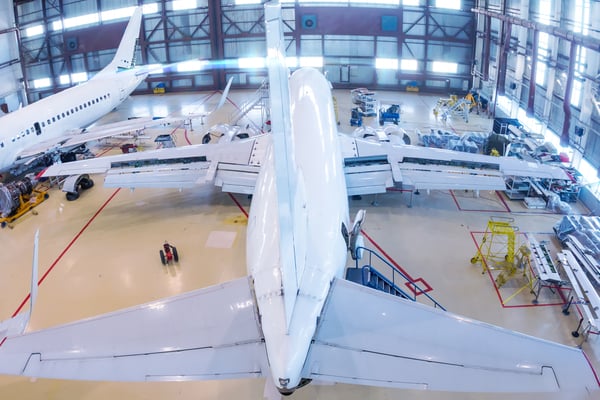
MRO Meaning in Aviation
Ever wondered what keeps the global fleet of aircraft, those marvels of engineering that crisscross our skies, operating safely and reliably day in and day out? While passengers might focus on the journey or the destination, ...
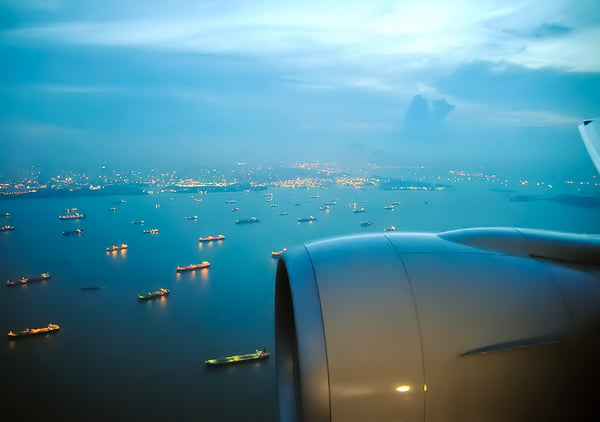
Engine Off-Wing? Understanding What Triggers an Aircraft Engine Removal
Aircraft engines are marvels of modern engineering, designed to operate reliably under extreme conditions. Yet, even these sophisticated machines require periodic removal for maintenance and overhaul. For airlines and maintenance ...
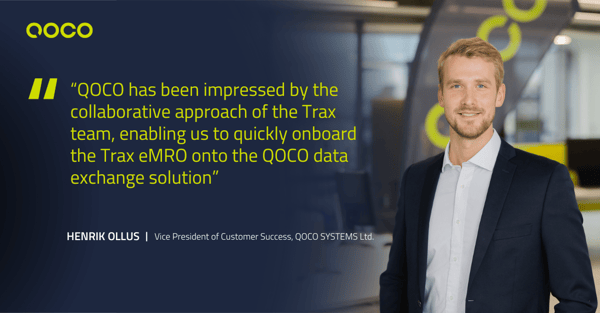
QOCO welcomes Trax as the next M&E system onto the QOCO data exchange solution for Rolls-Royce
ESPOO, Finland (April 9th, 2025) QOCO Systems, is delighted to announce Trax as the latest addition to connect to QOCO’s solutions, utilized by Rolls-Royce for its engine services. The Rolls-Royce and QOCO partnership began in ...
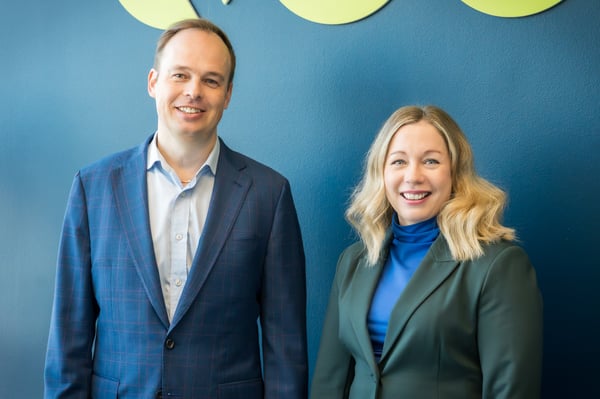
QOCO Systems expands its board with seasoned industry professionals
QOCO Systems welcomes Vesa Paukkeri and Emma Aidanpää-Salmi to the board as the company continues its aggressive growth within the aviation maintenance industry. The addition follows an announcement to increase staff with over ...