Realizing paperless maintenance and operations has been the target of airlines, MRO service providers (MROs) and OEMs in recent decades, especially in the last few years. With the increased adoption of electronic technical logbooks and digital solutions in maintenance, a growing number of airlines are getting close to going 100% paperless in their internal operations. However, that development is less well-advanced when it comes to external communication. Data sharing is essential for efficient collaboration in the industry, for example, in outsourced maintenance and component service activities, supporting digital twin initiatives and leasing agreements.
Room For Improvement
The potential for improvement is evident when considering the status quo in data sharing processes. Airlines, OEMs and MROs all manage asset data digitally in their own systems, but when the data is sent externally, it is exported onto a PDF or paper document. The receiving party then manually processes that data into their own system. In my view, the cause for the slow development in automation of data sharing in our industry can be traced down to the underlying dynamic. Namely, the party sending the data fulfills their contractual responsibility for sharing data when sending over a PDF or paper document, but the burden of manual data input is carried by the party receiving the data. To elaborate on this inefficiency and to consider potential solutions, I will next focus on data sharing in engine overhaul processes as a concrete example.
Engine Overhaul
When an engine is removed from the aircraft and sent for overhaul, the airline provides a number of documents to both the engine shop and the engine OEM. The bulk of the data contained in those documents concerns the engine assembly, modification status and utilization. To achieve an up-to-date snapshot of the asset status and to define the work scope for the overhaul, that data is manually entered by the engine shop and OEM operational teams into their respective systems. The obvious shortcomings of the process are the inefficient use of manpower, data quality issues due to human error and, in many cases, delays to maintenance work due to outstanding documentation from the airline.
The solution is, in theory, as obvious. An automated data sharing process, including human-in-the-loop elements, provides immediate tangible improvements to the status quo described above. In practice, this means data needs to be exported from the airline in a machine-readable format, and automated data import to the engine shop’s and OEM’s systems. In between, data transformation and validation are necessary. The manual effort is then reduced to confirming that the data in the airline system is up to date before initiating the export, and a review and approval of received data before it is accepted in the receiving system.
How data exchange works
This solution requires data export capability in the airline’s system, a data exchange solution to transfer, transform and validate the data, and import capability in the engine shop’s and OEM’s systems. For enabling the data exchange, industry-agnostic integration platforms will do the job, but there are a few IT vendors on the market that offer aviation- industry specific data exchange services, tailored for the data in this specific domain. The key question is then, why would the airline develop the required data export capability, when the solution mainly benefits the engine shop and OEM?
Depending on the existing capabilities of the airline’s Maintenance & Engineering (M&E) system, the automation of export and the data validations may be enough to justify the solution. In most cases, however, the airline will require a stronger value proposition. This value can be achieved by automation of the data flows in the other direction, from the engine shop to the airline after the shop visit. When the engine is returned, the engine shop typically provides the assembly, configuration and maintenance data to the airline in PDF format.
By automating the bi-directional data flows between the airline and engine shop before and after maintenance, substantial value is captured by both parties. In addition, the OEM can tap into this data flow to automatically keep its own system up to date. The figure below describes the architecture of these dataflows at a high level.
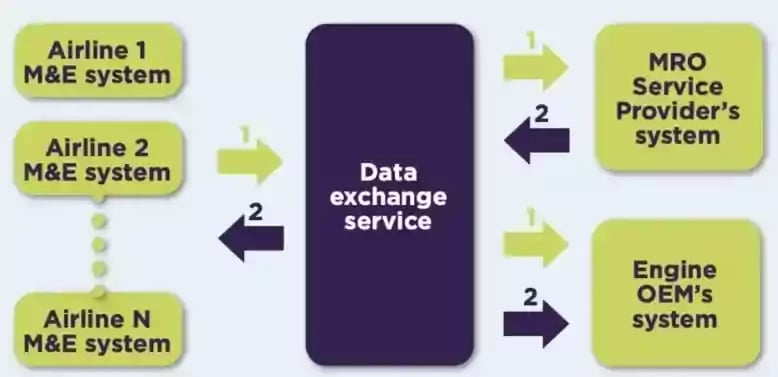
- 1 Data from the operator before the maintenance
- 2 Data from the Engine Shop after the maintenance
Getting data exchange implemented
The OEMs and maintenance service providers are better placed to champion this development, as they deal with a much larger number of engines. Nevertheless, the airline’s role in implementing the data export and import capability in their M&E system is essential. As the benefits to the airline are clear, but relatively fixed, their participation comes down to the implementation cost. This, in turn, depends heavily on the capabilities of the M&E system in use. Some M&E systems have separately licensed interfaces capable of exporting and importing the bulk of the required data, while others have no existing capability. To summarize, there is a clear underlying dynamic that explains the inefficient status quo of data sharing in our industry, but with close collaboration and the right partner for data exchange, considerable value can be created for the airlines, MROs and OEMs.
Experience seamless collaboration and eliminate manual data entry with Aviadex.io!